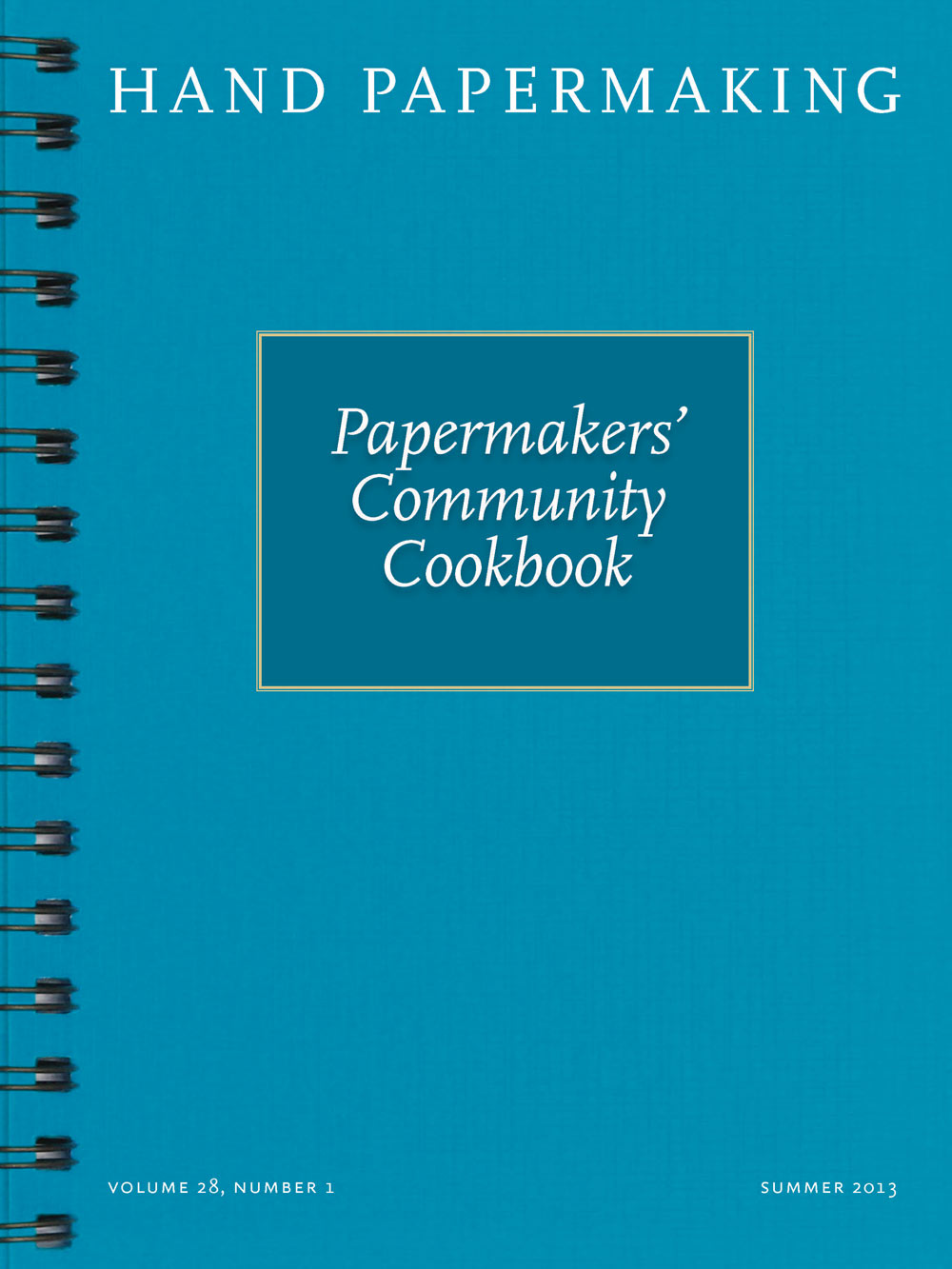
Summer 2013
:
Volume
28
, Number
1
Julie McLaughlin has been making paper and exploring paper's sculptural possibilities since the early 1990s. She shows her work—based on the corseted silhouette using handmade papers and welded, steel-rod armatures—both nationally and internationally. She is currently using her years spent as a theatre costume designer as a springboard for designing wearable handmade paper garments. Graduating from the University of Northern Iowa with a BA in art, she maintains a studio in Dysart, Iowa where she lives with husband Michael. I developed this marinade for my large, thin kozo sheets after being introduced to kakishibu while in residency at Luther College in Decorah, Iowa during the winter of 2007. Using Chris Conrad's book, Kakishibu, Traditional Persimmon Dye of Japan, as my guide, I started experimenting with my handmade kozo papers. I found that I could not incorporate the traditional methods spelled out in the book because of the fragility of my extremely thin, 6 x 9-foot sheets. After destroying many beautiful sheets by immersing them in a kakishibu bath, I blended the basic recipe found in the book with a different method of application and thusly my "marinade" was born.