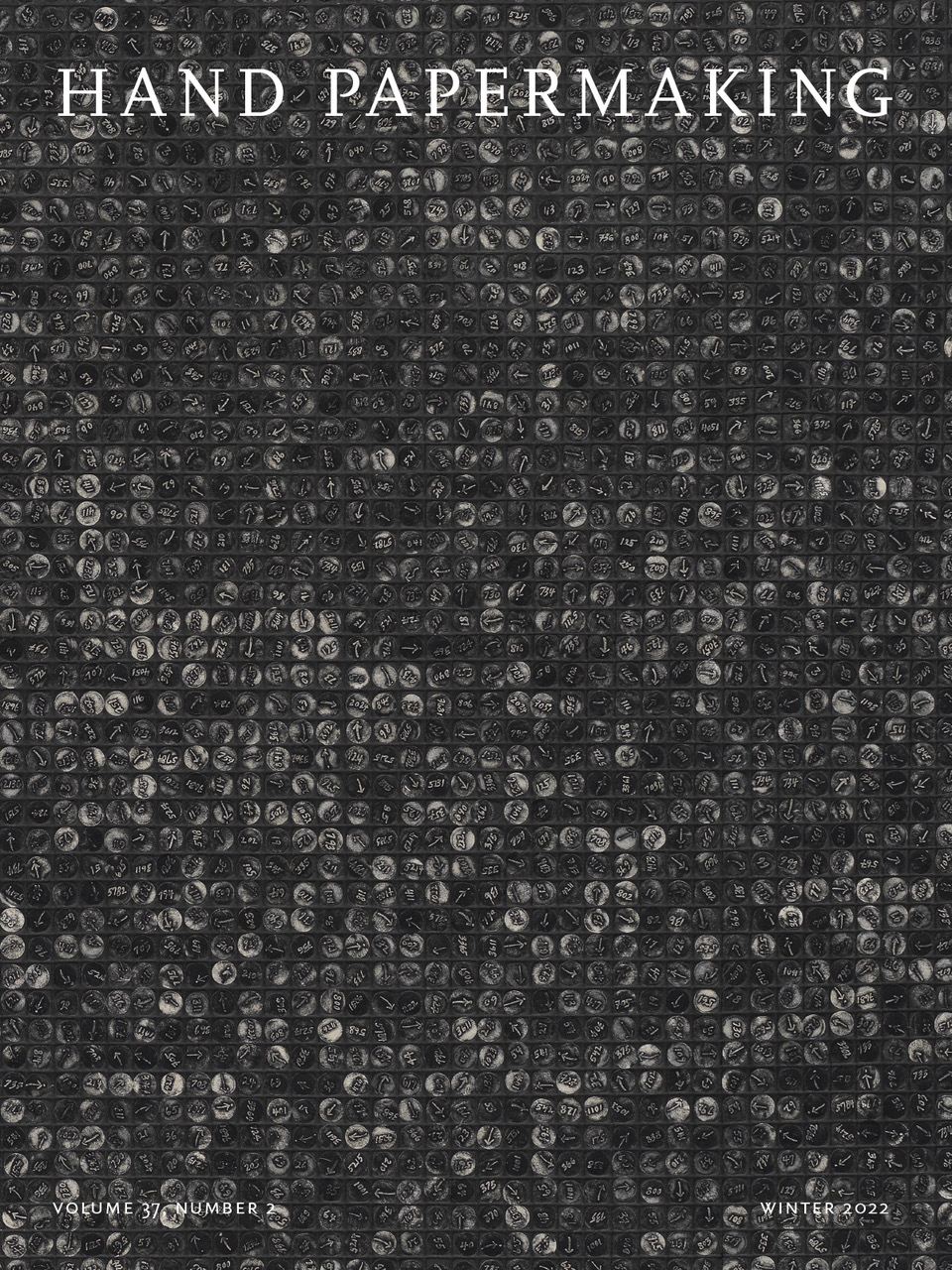
Winter 2022
:
Volume
37
, Number
2
This article is adapted from Thomas’s presentation entitled “Equipment I Have Developed,” which he delivered on September 25, 2021 at the 2021 (online) conference of the North American Hand Papermakers.
This article is adapted from Thomas’s presentation entitled “Equipment I Have Developed,” which he delivered on September 25, 2021 at the 2021 (online) conference of the North American Hand Papermakers.
This article is adapted from Thomas’s presentation entitled “Equipment I Have Developed,” which he delivered on September 25, 2021 at the 2021 (online) conference of the North American Hand Papermakers.
When I first decided to make paper in the spring of 1974, I was twenty years old, taking a year off from college and wanting to participate in an outdoor reenactment of an Elizabethan village market fair called the “Renaissance Pleasure Faire.” To find a role to play, I went to the library. There I discovered Dard Hunter’s Papermaking, The History and Technique of an Ancient Craft, and said to myself, “I will be Peter Papermaker, and teach people how to make paper.” Who would have known my simple wish to show folks how to make paper at a craft fair would develop into a lifelong passion.
Unbeknownst to me I was making paper during a huge surge of interest in hand papermaking that started in the US in the mid-1960s. Artists, mostly printmakers, were reinventing the craft to create unique artistic substrates for their work and to experiment artistically with paper and pulp. Working alone for the first few years I had to make my tools, acquire materials, and figure out how to use them to make paper. I finally started meeting other papermakers in the mid-1980s at conferences (FDH, IAPMA, and IPH). I shared what I had done and found that many of the same tools had already been made by others around the country; some that were much better than mine. I “stole” the better ideas, improving the tools in my shop as soon as possible. Although that was long ago, I still feel grateful for what I learned from others. As a way of repaying that debt I am writing this article about the tools in my shop, hoping that some of them might prove valuable to fellow papermakers.
on-demand water filter: I use city water with an in-line sediment filter hooked in before the hose bib. When filling my vat or beater I attach a second, charcoal water filter to my hose with a quick-release coupler.
shower-pan table: Beside my vat I mounted a metal shower pan—the floor part of a shower; plastic would be fine. I place a piece of light grating in it to keep the drain hole from getting blocked. I use this as a multipurpose table for draining the mould and discarding water with pulp in it. To filter out pulp before the water goes down my drain I connect a PVC pipe to the outflow underneath the pan (flex hose would also work) and secure a paint strainer bag to the end with big rubber bands.
shower-pan vacuum table: I also use the shower-pan table as a vacuum table to remove water from a slow-draining mould, to press a very thick sheet of paper, or to press a sheet that is larger than my hydraulic press. To do this, I remove the paint strainer bag and insert the hose of a shop vacuum. The fit needs to be airtight. I cobbled together adapters from a plumbing store, but closed-cell foam would also work. I put window screen over the light grating, then place whatever I want to vacuum on the window screen, and drape a thin piece of flexible plastic to cover it as well as the edges of the shower pan in order to create an airtight seal when the vacuum is turned on.
5-gallon blender: My Hollander beater jams easily if I add large sheets of cotton linters, abaca, or half stuff. To quickly break down sheet pulp I made a giant blender (like the one I saw that John Babcock made). I attached a ⅓ horsepower washing-machine motor to the bottom of a 5-gallon bucket. The motor’s shaft passes through the bucket and has a propeller attached to it. To stop the shaft penetration from leaking I glued a piece of rubber from a flipflop shoe, with a hole slightly smaller than the shaft, between the motor and the bottom of the bucket.
beater amp meter: I plug my Hollander beater into an amp meter (based on what I learned when visiting Douglass Howell). Mostly I use this to monitor how hard my beater is working so I can reproduce a recipe when making multiple batches of pulp for an edition book. I installed a meter that can register up to 20 amps, and hooked the hot wire from a female plug to one of the meter’s outputs and the hot wire from a male plug to the other output. I then connected the two plugs’ ground wires together and placed all of that in a wooden box to protect me from getting shocked. The beater plugs into the amp meter and the amp meter plugs into the wall.
dispersion bottle: As a way to assure even distribution of retention aid or sizing, I put the liquid in a plastic milk bottle. I punched small holes in the lid so that the resulting spray gives a wider distribution than just dumping in the liquid concentrate.
gas-tank vat: My vat is a stainless-steel gas tank that I repurposed from a boat. It has an angled side that I positioned running away from my body, so I could get my feet under the vat—the proper ergonomic position to have when making paper. Originally taking my cue from historic vats, I used a huge 100-gallon tank, but soon found that it was too large. It required endless beater loads of pulp to fill it, and when I was done making paper there were still too many beater loads of pulp left in it. So, I reduced the vat size to about 40 gallons, making it just deep enough to immerse my moulds without restriction.
agitator for vat: Many historic vats had devices to stir the water. Realizing how much effort that would save, after shortening my vat, I also installed a “hog.” Hog is the common term for a paddle-wheel device that rests near the bottom of the vat, close to and parallel to the papermaker’s body. I made mine by drilling perpendicular holes near each end of a 1-inch brass rod, pounding 4-inch pieces of smaller brass rods through those holes, then drilling holes in those smaller rods and bolting pieces of ⅛ x 1-inch stainless steel to each end in order to create four paddle blades. To mount the hog, I drilled holes through the side walls of the vat, about 3 inches from the front and bottom, then bolted on flush-mount, water-resistant bearings. To create a watertight seal—as I did with the 5-gallon blender—I sandwiched a layer of rubber flipflop material with a ¾-inch hole drilled through it between the bearings and the vat. The shaft of the hog runs through the bearings and is connected by a pulley and fan belt to a very slow-running motor. As the hog turns two things happen. First it stirs the pulp, allowing me to add pulp after forming each sheet; this helps to keep my sheets a consistent weight. Secondly it circulates the pulp from the front of the vat to the back, so when I dip in the mould, the pulp is effectively thrown onto the mould, which means I am lifting less weight, making a full day’s work much easier on the body.
mdo press boards & hydraulic couching stand: My press was originally used to laminate conveyor belts and has about 5 inches of daylight. I couch onto press boards made from MDO plywood, also known as “sign painter’s board.” MDO does not have voids; it is paper faced and completely waterproof. The paper surface assures that you do not get wood splinters in your felts. Even a 5-inch post is too heavy to lift when making 18 x 24-inch sheets so I put my press boards on a hydraulic lift table (purchased from tool or auto supply stores). This allows me to both adjust the height of the post while couching, and to raise the completed post to the level of the press.
stack dryer: My version of a forced-air stack dryer has the following layers: double-wall corrugated cardboard, mat board, blotter, damp sheet, blotter, binder board, double-wall corrugated cardboard. The binder board helps maintains the integrity of the cardboard by eliminating direct contact with moisture migrating from the wet paper and blotters, which is the main cause of cardboard warping and the air channels collapsing. Any thin board can be substituted for binder board; it does not have to be archival because the water is migrating out of the handmade paper. I have used the same sandwich of materials for over 20 years and thousands of sheets.
modified dry-mount press: To dry a single sheet of handmade paper (when I am checking color or trying to determine the right paper weight), I use a dry-mount press that I modified (based on one used at Magnolia Editions) by replacing the big rubber pad in the base of the press with a piece of aluminum that has channels cut length-wise; it could also be made from hard rubber or plastic. I cover this with a piece of perforated aluminum plate, and place two felts on top. Then I put the wet sheet of paper between two blotters and place the sandwich on top of the felts. I close the press until I feel light pressure being applied to the layers. I heat the press to about 220 degrees Fahrenheit, and run a fan at one end to blow out the moisture that comes out of the paper, through the blotters and felts, and into the channels, as the paper is drying.