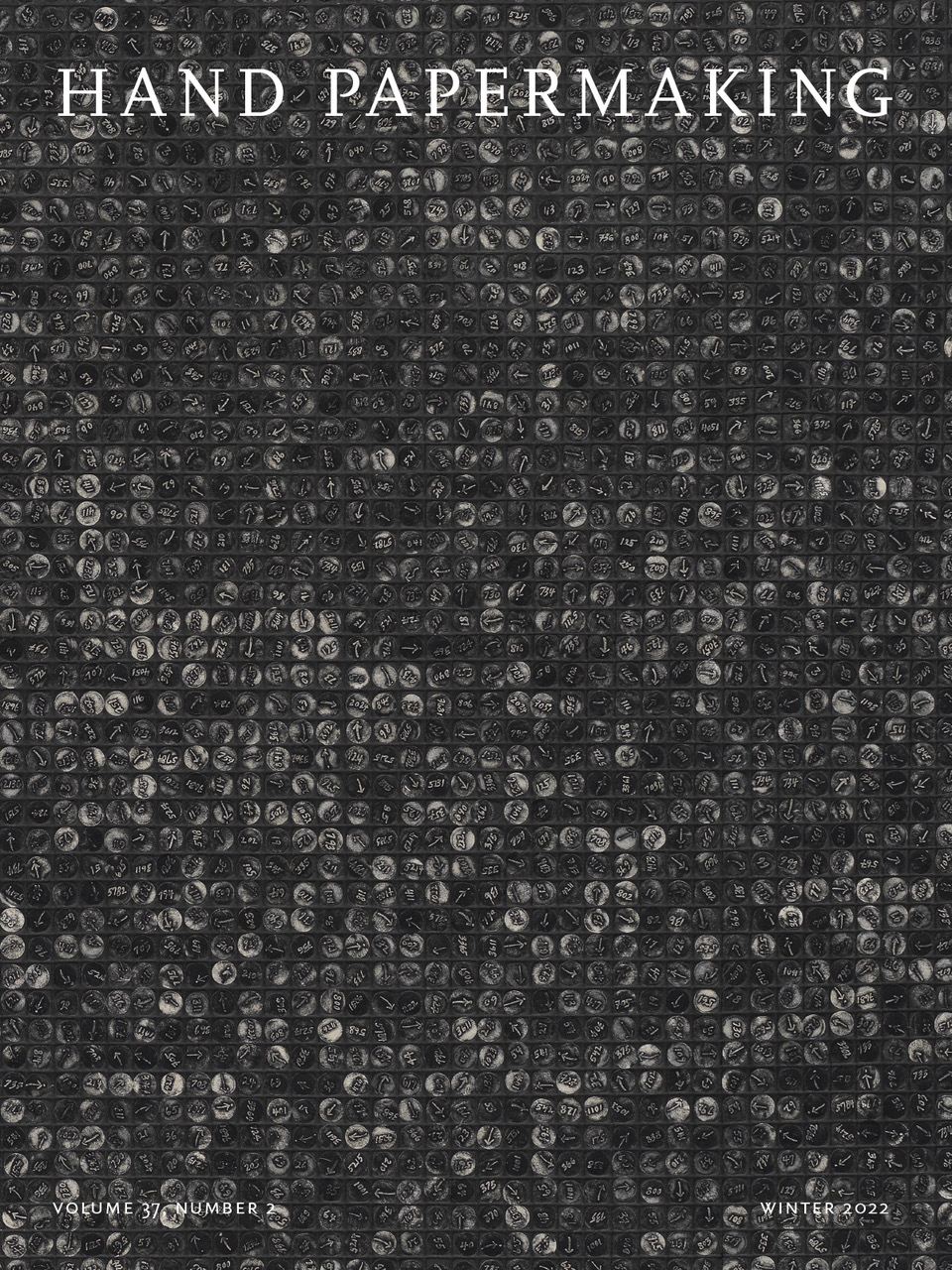
Winter 2022
:
Volume
37
, Number
2
In the studio I use a variety of materials to make watermarks and embossments, as a way to create space in paper.
In the studio I use a variety of materials to make watermarks and embossments, as a way to create space in paper.
In the studio I use a variety of materials to make watermarks and embossments, as a way to create space in paper.
I make watermarks from metal wire and cut metal plates that I sew or solder onto the mould surface. I also use 3-D pens, 3-D printing, or lace and other materials that I place on top of the mould. I like these alternative methods because they do not require soldering or sewing to the mould surface. This saves a lot of time and feels spontaneous compared to manufacturing a traditional watermark. In exploring different ways to create surface designs in papermaking, I discovered a lot of interesting techniques.
Once, when I had trouble couching a wet sheet off a papermaking mould that I covered with lace, I put the sheet and the lace into the stack dryer and recognized that the lace created a wonderful blind embossing, crisp and precise.
Another watermarking stencil that has a lacy design is a rubber material used for making placemats; I source this material from a French company. The regular distribution of the netlike design is helpful while forming a sheet because the water drains evenly across the mould. Look for designs that do not have large areas of rubber material where water has a hard time draining; those can result in holes in the paper.
In the Department of Book and Paper at the University of Applied Arts, Vienna, I worked with students to explore how words can be brought into and on paper to create limited-edition and one-of-a-kind artist books. I created a range of paper samples introducing text with embroidery, laser cutting, burning, stamping, watermarking, embedding letters between two sheets of wet paper, and so forth.
The artist and former student Isabella Kohlhuber, who is focused on typography in her artwork, laser cut embossing stencils out of black rubber that is typically used for bike wheels. The rubber left a black residue on the paper; later we came up with a source of rubber that that did not rub off. The thickness of the material determines the depth of the embossing; it should be 1 millimeter thick or more. Isabella designed the image digitally in a vector program for the laser cutter. She left a margin of 1.5 centimeters all around the design so that the deckle can hold the stencil firmly in place. With this type of stencil, we made two-layered sheets to create a “watermark”: one with the block-out design; and the other as a base sheet.
To make the stenciled paper, I recommend cotton half stuff and a base sheet made of transparent abaca. Cotton half stuff has a longer fiber length than cotton linters; this helps to form a strong matrix of fibers in the final sheet. I beat the cotton half stuff for an hour in the Hollander beater. You can add sizing and calcium carbonate as well. For a well-defined image, fill the vat with a lot of pulp to create thick sheets. For best results, the mould should have a very flat surface and everything should be wet: the stencil, the mould, the felts. To avoid getting pulp underneath the stencil, dip the mould into the vat with a deep vertical angle. Move the mould through the water at the same speed as the water flowing towards the mould from the back side. After lifting the mould out of the vat, shake it vigorously so the pulp flows into the open areas of the stencil. Remove the deckle and let everything drain well. When couching, hold onto the stencil with your fingers so it does not fall off the mould when you release the stenciled sheet onto a felt. When you hold the finished sheet up to the light, the design will be opaque against the base layer of transparent abaca.